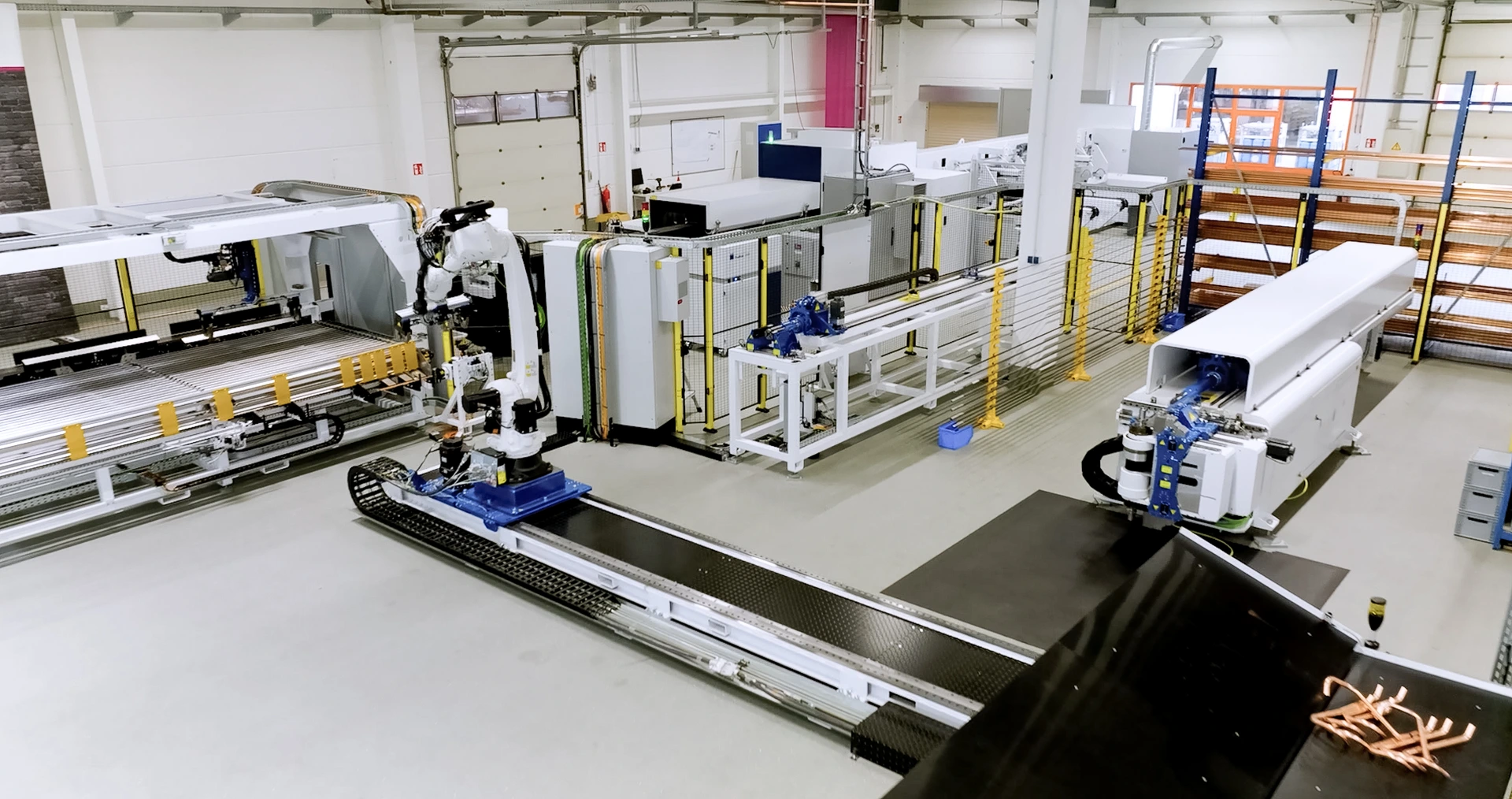
CUSTOMER STORY:
ALL GOOD THINGS COME IN THREES.
Highly flexible combination between laser tube cutting system and tube bending technology.
Automated tube process chain at TEKO GmbH
Teko GmbH, based in Altenstadt/Hesse, is an internationally successful supplier of refrigeration systems for food chains and industry. With a workforce of 250, Teko has been producing composite systems, refrigeration components and control electronics for more than 40 years.
More than 80 kilometres of copper tube are processed each year for the 12,000 different tube geometries that are now available, and the trend is rising. One of the main reasons for planning a new automated tube production system was to be able to produce these geometries with one system, in addition to the increasing shortage of skilled labour.
High flexibility, customer-specific handling, a high degree of automation for copper tubes from 6 to 42 mm in diameter and chipless cutting were the specifications with which Teko approached the tube bending and tube processing machine specialist transfluid Maschinenbau GmbH. The company was looking for a solution that would reduce the number of soldered joints, avoid capacity bottlenecks and eliminate the high cleaning costs caused by chips.
The partnership between transfluid and Trumpf has taken the project a decisive step forward. Thanks to the use of a laser tube cutting system, no chips are produced when cutting the tubes, which means that the effort required for post-cleaning the tubes is significantly reduced.
THE SOLUTION
The solution was to cut the tubes with a TRUMPF Trulaser Tube 5000 and then transfer them automatically to the transfluid bending cell. The bending cell includes a conveyor section that can buffer up to 25 tubes of different lengths pre-cut by the laser. A robot transfers the tubes to a brushing station for cleaning and then to the bending machine. Tubes from 200-4500 mm in length can be processed in the bending cell. The TRUMPF nesting programme takes the data from the T project bending software from transfluid. This means that different lengths and diameters for different geometries can be produced in a single production run.
A transfluid t bend DB 642 CNC RL bending machine is used to provide this flexibility. The CNC-controlled bending machine with rotating bending head can bend steel, stainless steel and non-ferrous metal tubes as round tubes or profiles from ø 6-42 mm. And with tube lengths up to 4.5 metres. The bending head can be positioned horizontally or vertically, including an axis of rotation to change the bending direction. The electrically driven bending machines are designed for high volume production and are energy efficient thanks to economical servo technology.
The 12 electric axes can be programmed synchronously to achieve optimum cycle times. Multi-plane bending tools with automatic tool change enable a wide variety of parts to be bent.
THE SOFTWARE
The new transfluid bending software t project 5.0 takes tube processing to the next level with ground-breaking features such as the digital twin, offline programming and CloudDrive. With t project, bending processes can be quickly and accurately planned and fully simulated. The 'digital twin' virtually maps the entire bending process, making it possible to check for collisions and optimise cycle times even before production.
New to t project are product databases of complete tube assemblies, which provide a comprehensive visualisation of holes, shapes and nuts. This allows even more precise planning and execution of complex geometries.
Offline programming means that programmes can be created and tested independently of the machine, saving valuable production time and increasing flexibility.
In combination with the Trumpf Programming Tube software, this opens up completely new possibilities for tube processing. Cutting processes can be precisely planned and efficiently executed - ideal for complex geometries in refrigeration plant construction. The comprehensive automation functions, such as intelligent nesting and optimised cutting paths, result in noticeable material savings and optimised production times.
As a result, the t bend DB 642 RL and the TruLaser Tube 5000 can be used to their full potential, ensuring maximum quality and cost-effectiveness.